It’s rare that businesses selling equipment to the oil & gas sector can benefit from lower oil prices.
Lower oil prices and national-level oil production quotas have contributed to a strategic shift among major Middle Eastern national oil companies (NOCs) towards natural gas development. As Saudi Arabia, the UAE, Kuwait and Oman develop their natural gas industries, the NOCs are increasingly requiring piping equipment capable of handling high pressure and sour gas, with hydrogen sulphide and carbon dioxide content frequently encountered and requiring engineering attention.
While corrosion resistant alloys (CRAs) have been used for many years in oil & gas production throughout the region, the current level of demand and project pipeline has never been seen before; in the GCC or anywhere else in the world. When the Kashagan project required 60 kT of clad pipe material it was considered exceptional due to the widespread equipment failures in that project. When the under-construction Barzan project required 90 kT it was considered exceptional due to design and equipment failures, and required hasty capacity increases in the manufacturing facilities of the project winners. Now with the design phase of Hail & Ghasha progressing towards completion, with indications that another 50 kT of clad and other CRA pipe will be required for this project alone (volume unconfirmed at the time of writing), the impact of under capacity is being felt by oil companies around the world. Demand has increased smartly since 2014 and is anticipated to remain at an elevated level for the next five years, with the sector now yearning for investment.
One consequence of project developers’ concern around clad pipe capacity limitations – and associated capacity for substrate material – is an increase in anticipated demand for weld overlay CRA pipe. As a manufacturing method, weld overlay has historically contributed relatively low volumes within the industry, requiring far higher lead times and with hints of concern around ease of repair and maintenance. This appears to be changing, with project developers increasingly comfortable using this method for lower tonnages of CRA pipe, in addition to the bespoke applications and processing equipment used alongside. This is particularly true in the high volume Middle East market where weld overlay methods are widely accepted.
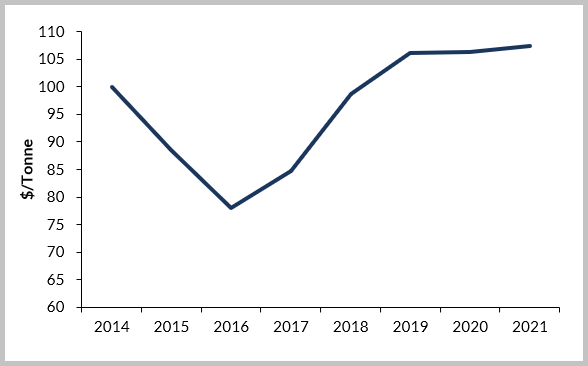
Source: Westwood Analysis, Fastmarkets
The impact of a broader demand/supply imbalance is already affecting pricing, material selection, project schedules and supplier relations. Other manufacturing methods for CRA pipe, including mechanically lined and solid alloy pipe, are expected to benefit. These will contribute tonnage to projects that may have historically used carbon or clad pipe, where feasible.
CRA pipe manufacturing is a rare area of the oil & gas equipment market that is comfortably outperforming 2014 levels. For much of the supply chain, oil prices at the current level will work just fine.
Westwood Global Energy, alongside Fastmarkets, have now included analysis of the weld overlay market in the recently launched update to the Future of Corrosion Resistant Alloys Service, with a focus on CRA pipe.
Matt Loffman, Associate Director, Rigs & Wells
[email protected] or +44 (0)203 4799 505